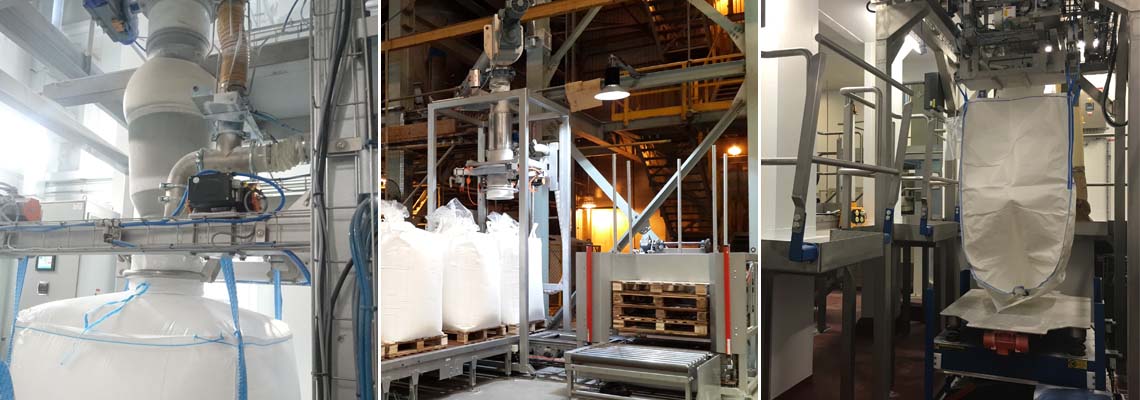
Na maioria das aplicações industriais, há duas razões principais pelas quais uma fábrica investe em uma estação automatizada de enchimento de big bags:
- Minimizando a intervenção do operador
- Para atender ao aumento da demanda de produtos/ metas de rendimento
Quais são os diferentes equipamentos para a implementação de um sistema de enchimento de big bags de alta velocidade?
1. Tremonha amortecedora de pesagem
Os funis-tampão pesados que alimentam as máquinas de embalagem de big bags são um dos componentes mais importantes nos sistemas de alta produtividade. Estes tanques de pó são usados para armazenar temporariamente pós e grânulos para garantir a alimentação precisa e controlada do processo de produção.
Os componentes mais comuns usados nas tremonhas de pesagem são sondas de alto nível, sondas de baixo nível e células de carga (também chamadas de células de carga). As sondas de nível são usadas para indicar o nível de enchimento do funil para o equipamento a montante e assim ativar o enchimento ou esvaziamento do funil.
A fim de obter automaticamente um peso de enchimento preciso nos big bags a jusante, as células de carga são instaladas sob os suportes do funil. Estas células de carga são tipicamente utilizadas em sistemas que utilizam a função "ganho de peso" ou "perda de peso".
As células de carga indicam ao sistema de controle que o peso alvo do pó foi alcançado no funil. Quando se trata de um sistema automático de enchimento de big bags que requer altas taxas de embalagem de big bags, os funis amortecedores de ganho de peso duplo funcionarão sequencialmente.
Quando os funis amortecedores de ganho de peso são instalados próximos uns dos outros e alimentam a mesma estação de enchimento de big bags, o primeiro funil contendo o pó pode descarregar no saco grande enquanto o segundo funil está sendo enchido. Ao trabalhar desta forma em tempo mascarado, há sempre um funil cheio pronto para encher a big bag.
Os funis-tampão pesados são normalmente dimensionados de acordo com a densidade do pó a ser manuseado e a capacidade do big bag a ser enchido. As válvulas borboleta ou válvulas de gaveta são instaladas na saída do funil para controlar o fluxo de pó.
Outros componentes podem completar a instalação. De fato, auxiliares de fluxo como motores vibratórios, bicos de jato de ar, martelos pneumáticos, etc. ajudam a evitar problemas de aglomeração ou ponte ao lidar com pós que tendem a fluir mal.
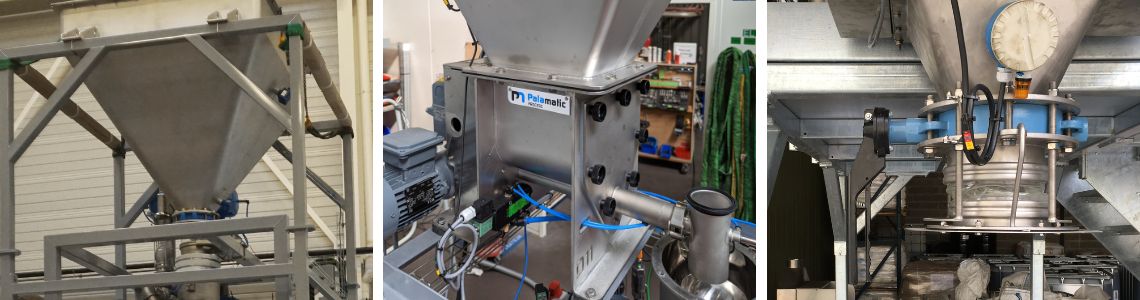
2. Equipamento de controle de fluxo e dosagem de pó
Outro elemento chave para alcançar altas taxas de enchimento debig bags é como o pó é manuseado e dosado uma vez que deixa o funil de alimentação a montante.
Como mencionado anteriormente, uma válvula borboleta ou uma válvula de guilhotina é normalmente usada como a válvula principal para controlar o fluxo de pó para fora do funil.
A partir deste ponto, como o pó flui através de uma calha de alimentação por gravidade até a estação de enchimento abaixo, ele pode ser direcionado para um dos dois dutos.
O duto principal é o duto de alto fluxo. É freqüentemente complementada por válvulas borboleta logo acima e abaixo dos canais.
Quando o big bag é cheio a 95% de sua capacidade total, a válvula borboleta na parte superior do duto de alto fluxo fecha e desvia o pó para a rosca alimentadora. A rosca alimentadora proporciona precisão repetitiva na dosagem do pó. Consiste em um funil integrado com um agitador que alimenta um tubo. Dentro do tubo há um pequeno parafuso que empurra o produto para a extremidade da saída em direção ao processo a jusante. Estes alimentadores de rosca oferecem uma boa precisão de dosagem de até -/+ 1-2 gramas.
Outro tipo de sistema de dosagem de pó que pode ser usado é o dosador vibratório. Os alimentadores vibratórios utilizam motores vibratórios e a estrutura é apoiada por molas que permitem que a unidade vibre. A calha tem uma inclinação mínima que permite à unidade mover o material em direção ao final da calha para alimentar o processo a jusante.A taxa de alimentação pode ser controlada aumentando ou diminuindo a amplitude e a freqüência das vibrações.
Este tipo de alimentador de pó ajuda a manter a integridade do produto ou evitar o desgaste desnecessário no caso de materiais abrasivos. O alimentador de rosca é operado para os últimos 5% do objetivo de enchimento de sacos grandes. Ao utilizar um alimentador fracionado como descrito acima, os sistemas automatizados de enchimento podem encher big bags de forma rápida e eficiente com precisão.
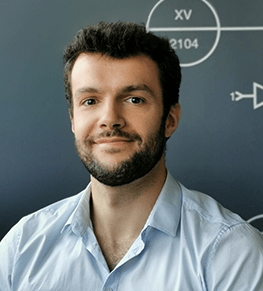
Você tem um projeto? Estou disponível para
aconselhá-lo e acompanhá-lo em seu estudo.
Paul, especialista em pó
3. Contenção e controle de poeira
Uma das peças de equipamento mais essenciais para qualquer instalação de produção industrial é a coleta e filtragem de pó. Também é essencial que todos os equipamentos de manuseio sejam projetados para operar de forma estanque ao pó e conter os pós que estão sendo manipulados. Os riscos são significativos: toxicidade do material e exposição aos operadores, acidentes por deslizamento e queda devido à presença de pó e poeira no piso, falha mecânica do equipamento, relação ar/poeira da mistura levando a uma explosão, etc.
Há vários tipos de coletores de pó a serem considerados:
- Sistemas centralizados de coleta de pó para todos os equipamentos de produção. Estes incluem filtros de saco de tecido, separadores inercial (como ciclones mecânicos), filtros úmidos, coletores de cartucho e precipitadores eletrostáticos
- Unidades de filtro de pó integradas a equipamentos específicos: por exemplo, filtro de pó integrado na parte superior de uma estação de esvaziamento de sacos
- Filtros de desgasificação
- Capuzes para extratores
- Anéis de coleta de pó (anéis Pouyes): em cima de um tanque de armazenamento, por exemplo, onde os operadores alimentam manualmente os sacos de pó.
As unidades de coleta de pó são normalmente equipadas com cartuchos de filtro montados lateralmente ou na parte superior. Estes filtros são conectados a um tanque de ar comprimido externo, configurado em um ciclo temporizador. Quando a poeira passa pelo filtro, um jato de ar intermitente é enviado do lado oposto para limpar o acúmulo excessivo de poeira. Este sistema de limpeza por jato de pulso invertido tem duas funções:
1. evita o entupimento dos filtros sem necessidade de manutenção
2. Ele ajuda a recuperar o produto que escapou nos filtros.
Ao encher sacos grandes, é importante que a conexão entre a cabeça de enchimento e a calha do saco grande seja segura e à prova de poeira.
O método mais comum é usar um selo de inchaço na cabeça de enchimento. O operador posiciona a calha do saco grande ao redor do selo de elastômero. O ar pressurizado é introduzido no selo, fazendo com que ele incha e mantenha o pára-quedas firmemente no lugar.
A cabeça de enchimento também pode ter uma jaqueta dupla (um tubo interno rodeado por um tubo externo). O canal interno permite a passagem do pó e o saco grande a ser enchido. O canal externo permite a fuga de ar e poeira muito leve através de uma peça de conexão. Este espigão pode ser equipado com uma manga de filtro ou com uma mangueira que se conecta a um coletor central de pó. Em unidades de produção que processam materiais particularmente tóxicos, tais como pós de lítio na indústria de fabricação de baterias, toda a instalação pode ser instalada em um invólucro projetado para extrair um vácuo atmosférico constante para um sistema externo de coleta de pó.
4. Tabela de densificação vibratória e células de carga
Um dos problemas mais comuns no transporte e armazenamento de big bags cheios de pós e materiais granulares é a falta de estabilidade. Isto se deve ao fato de que as partículas de pó são muito "aeradas" durante o processo de enchimento.
Quando o material se instala por gravidade por si só, pode ocorrer a separação de partículas. Como resultado, as partículas finas caem para baixo e as partículas maiores permanecem em cima.
Isto pode causar a queda do big bag e a inclinação para um lado, resultando em alta instabilidade durante a movimentação ou empilhamento durante o armazenamento.
As mesas vibratórias de aumento de tensão são um componente necessário de qualquer linha de produção semi-automática ou totalmente automatizada de enchimento de big bags.
À medida que o saco a granel se enche de material a granel, a mesa de densificação vibra de forma intermitente. Esta vibração permite que pequenas bolsas de ar entre as partículas escapem, apertando assim as partículas juntas. Isto limita a segregação de partículas e torna o big bag mais rígido e, portanto, mais fácil de transportar e armazenar.
Além disso, a instalação de um transdutor de força sobre esta mesa vibratória converte uma força como tensão, compressão, pressão ou torque em um sinal elétrico que pode ser medido e normalizado. Conforme a força aplicada à célula de carga aumenta, o sinal elétrico muda de acordo.
As células de carga ou células de carga são conectadas a um controlador lógico programável (CLP) que lê a quantidade de peso que entra em um big bag durante a seqüência de enchimento.
Um peso alvo é programado no painel de controle. Quando as células de carga indicam que o big bag está quase completamente cheio, o CLP envia um sinal para a unidade dosadora de pó (rosca dosadora, válvula rotativa) para diminuir a velocidade e despejar os últimos 5% do peso alvo.
Quando o peso alvo é atingido, as células de carga enviam um sinal para o CLP que diz à válvula para fechar e parar o enchimento. Utilizando células de carga, podemos automatizar a seqüência de enchimento sem a intervenção de um operador e assim obter um peso de enchimento muito preciso.
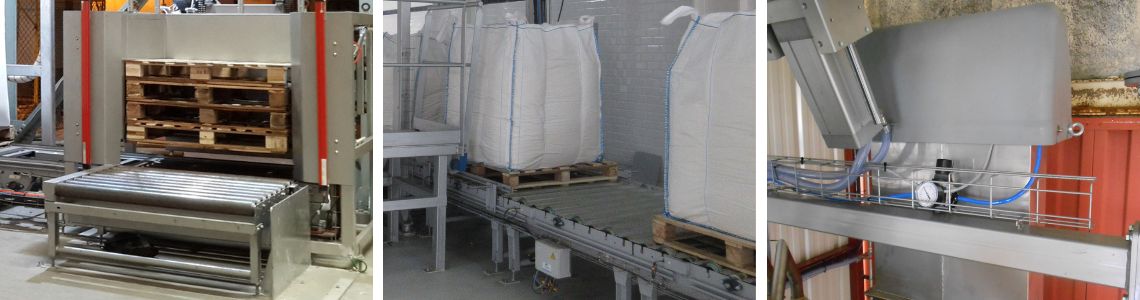
5. Descofrador de paletes e transportador mecânico de rolos
Os dois componentes finais essenciais para automatizar sua linha de enchimento FIBC são desempilhadores de paletes e transportadores mecânicos de rolos.
Os desempilhadores de paletes utilizam braços indexadores robóticos conectados a cilindros pneumáticos que podem levantar, baixar e posicionar um palete em uma estação de enchimento.
Eles podem segurar até 20 paletes de cada vez. A máquina alimenta um palete a cada 35 segundos e pode ser projetada para acomodar diferentes tamanhos de paletes. Cada vez que um grande saco é preenchido, o CLP pode dizer ao desempilhador de paletes para posicionar o próximo palete no transportador mecânico de rolos.
Os transportadores mecânicos de rolos têm várias funções diferentes, mas são utilizados principalmente neste caso para transferir os paletes para a estação de enchimento e depois descarregar o big bag completo para uma área de armazenamento de reserva. Um operador então pega o saco grande cheio com uma empilhadeira e o transporta para a área de armazenamento final. Todos os parâmetros e seqüências são controlados pelo CLP, o que elimina qualquer trabalho manual. Os rolos transportadores são espaçados uniformemente e são acionados por um motor de engrenagem localizado na lateral, ou por gravidade em um ângulo de inclinação mínimo. Os transportadores de rolos por gravidade têm rolos de controle de velocidade que são usados para controlar a velocidade da carga a ser transportada, tais como um big bag em seu palete em nosso caso. Independentemente do tipo de transportador, eles operam em seqüência para fornecer um fluxo constante de grandes sacos de e para a estação de abastecimento.
Com estes dispositivos, as operações de enchimento de big bags minimizam o número de operadores em uma única estação de trabalho.