Transição para uma produção flexível: adote contêineres IBC para uma gestão eficiente de pós
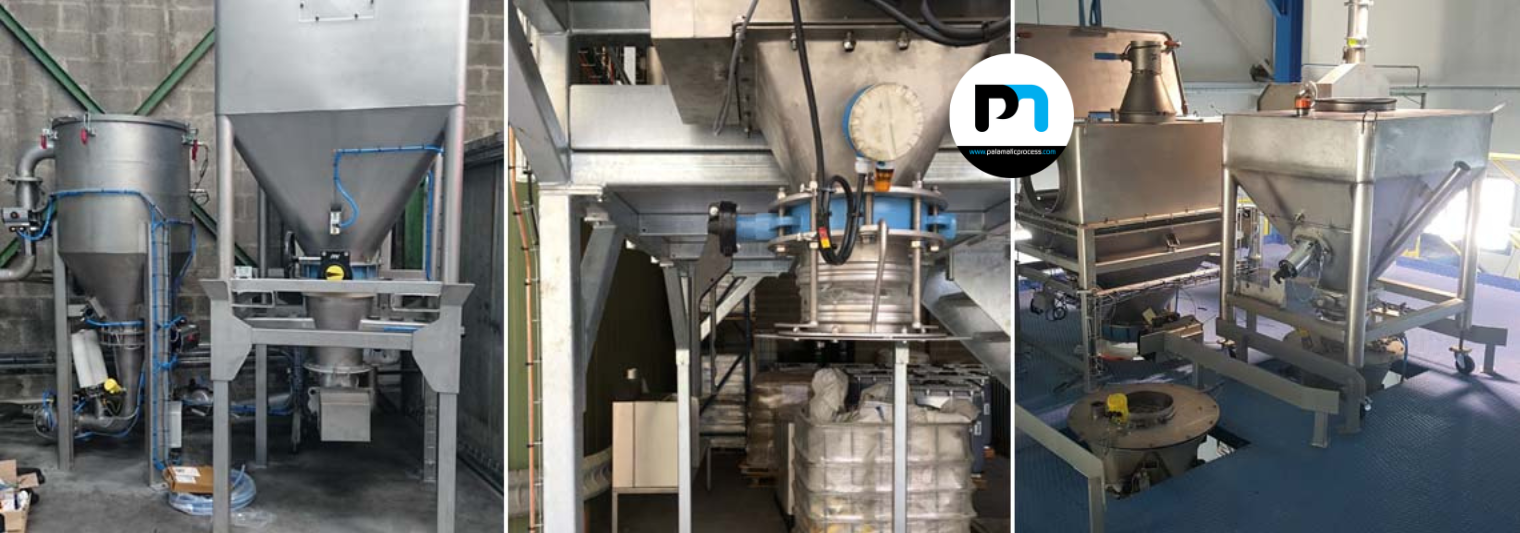
- 1. Por que considerar uma transição para contêineres IBC ?
- 2. Perguntas preliminares para uma transição bem-sucedida
- 3. Dimensionamento de equipamentos e integração de contêineres IBC
- 4. Restrições e soluções para o esvaziamento de contêineres IBC
- 5. FAQ: Respostas às perguntas mais frequentes sobre a transição para contêineres IBC
- 6. Conclusão
Os setores alimentício, farmacêutico e de cosméticos estão migrando para soluções de produção mais limpas e automatizadas.
O gerenciamento de pós em sacos grandes e sacolas apresenta uma série de restrições: manuseio repetitivo, emissões de poeira e contaminação cruzada. As soluções Full IBC oferecem uma alternativa confiável e flexível.
Elas garantem um manuseio simplificado, melhor rastreabilidade e fácil integração em processos automatizados.
Mas como fazer a transição? Quais critérios precisam ser considerados?
Como dimensionar o equipamento e otimizar o esvaziamento dos contêineres IBC? Este artigo detalha as etapas essenciais para adotar uma produção mais eficiente e higiênica.
1. Por que considerar uma transição para contêineres IBC ?
1.1. Limitações dos métodos tradicionais
Os métodos tradicionais de manuseio de pós, embora ainda sejam amplamente usados, têm grandes desvantagens que afetam a produtividade e a qualidade das operações industriais.
Manuseiopesado e riscos ergonômicos: o manuseio de big bags exige o uso de equipamentos específicos, como guinchos ou empilhadeiras. Essas operações não apenas impõem uma carga física pesada aos operadores, mas também representam um risco significativo de acidentes no local de trabalho. Movimentos repetitivos e posturas incômodas podem levar a distúrbios musculoesqueléticos (MSDs), a principal causa de doenças ocupacionais na indústria.
Tempos de troca de lote mais longos: A troca de um lote de produção para outro usando sistemas tradicionais envolve uma grande quantidade de manuseio: remoção de sacos vazios ou sacos grandes, limpeza de equipamentos e instalação de novos contêineres. Essas operações podem representar até 20% do tempo total de produção, reduzindo significativamente a produtividade da linha.
Contaminação cruzada e problemas de higiene: Os sistemas abertos incentivam a emissão de poeira e o risco de contaminação entre produtos diferentes. Em setores sensíveis, como o farmacêutico e o alimentício, esses problemas podem ter consequências graves para a qualidade do produto final e para a segurança do consumidor.
Impacto ambiental: o uso de sacolas e, em menor escala, de big bags gera uma quantidade significativa de resíduos. As sacolas de papel ou de plástico geralmente são de uso único, o que vai contra os objetivos de desenvolvimento sustentável que cada vez mais empresas estão estabelecendo.
Rastreabilidade limitada: os sistemas tradicionais oferecem rastreabilidade limitada do produto em toda a cadeia de produção. A identificação manual de lotes e as múltiplas transferências de produtos aumentam o risco de erros no rastreamento de matérias-primas e produtos acabados.
1.2. Vantagens dos IBCs
Os IBCs representam uma alternativa moderna e eficiente que aborda diretamente as limitações dos métodos tradicionais e oferece benefícios adicionais.
Hermético e higiênico: o design fechado dos IBCs evita a liberação de poeira e protege o produto contra contaminação externa. Os modelos de aço inoxidável oferecem superfícies lisas que são fáceis de limpar e desinfetar, atendendo aos mais rigorosos padrões de higiene dos setores farmacêutico e alimentício.
Facilidade de manuseio e ergonomia: Projetados para serem movimentados facilmente por meio de paleteiras ou sistemas automatizados, os contêineres IBC reduzem consideravelmente o esforço físico exigido dos operadores. Seu formato padronizado e suas dimensões otimizadas facilitam o armazenamento e o manuseio, melhorando as condições de trabalho e a segurança.
Integração em linhas automatizadas: Os contêineres IBC são perfeitamente adequados àautomação. Eles podem ser equipados com sistemas de identificação (RFID, códigos de barras) para rastreamento em tempo real. Essa compatibilidade com as tecnologiasda Indústria 4.0 abre novas oportunidades em termos de gerenciamento de produção e otimização de fluxo.
Esvaziamento controlado e seguro: sistemas de esvaziamento específicos, como oIBCFlow®02, permitem que os pós sejam descarregados de forma controlada, limitando as emissões e garantindo a transferência completa do produto. Tecnologias avançadas, como válvulas borboleta ou sistemas de aba dupla, garantem uma vedação perfeita durante todas as fases de manuseio.
Tempo de inatividade reduzido: o uso de IBCs otimiza as trocas de lotes e reduz o tempo de limpeza. Um contêiner vazio pode ser imediatamente substituído por um cheio, garantindo a continuidade da produção. Essa flexibilidade operacional se traduz em um aumento significativo nas taxas de utilização dos equipamentos.
Durabilidade e retorno do investimento: Construídos para durar, os IBCs de aço inoxidável podem ser usados por décadas com manutenção mínima. Embora o investimento inicial seja mais alto do que o das soluções de big bag, elese paga rapidamente por meio da economia de consumíveis e do aumento da produtividade.
Rastreabilidade otimizada: cada contêiner pode ser identificado individualmente, permitindo o rastreamento preciso do lote durante todo o processo de fabricação. Essa rastreabilidade aprimorada facilita o gerenciamento de recalls de produtos e a conformidade com requisitos regulatórios cada vez mais rigorosos.
2. Perguntas preliminares para uma transição bem-sucedida
2.1. Natureza dos produtos manuseados
Uma transição bem-sucedida para o uso de IBCs depende, em grande parte, de uma análise aprofundada das características dos pós manuseados. Essas propriedades determinarão não apenas o tipo de contêiner a ser preferido, mas também o equipamento auxiliar necessário para o gerenciamento ideal.
Tamanho e distribuição das partículas: O tamanho das partículas tem influência direta sobre o comportamento do fluxo dos pós. Os produtos com partículas finas (menos de 100 mícrons) geralmente são mais coesos e podem exigir auxiliares de fluxo. Por outro lado, os pós com tamanho de partícula mais grosso fluem mais livremente, mas podem estar sujeitos à segregação durante o manuseio. Uma análise completa do tamanho das partículas deve incluir não apenas o tamanho médio das partículas, mas também a distribuição (extensão e forma da curva de tamanho das partículas). Uma distribuição estreita ou bimodal pode influenciar significativamente as propriedades de fluxo e a compactação do produto.
Densidade a granel e de vazamento: a densidade dos pós tem um impacto direto na capacidade dos IBCs. Um pó de baixa densidade exigirá um contêiner de maior volume para a mesma massa de produto. Conhecer a relação entre a densidade de vazamento e a densidade aparente (índice de Hausner) nos permite avaliar a compressibilidade do pó e prever possíveis problemas de compactação durante o transporte.
Comportamento reológico: as propriedades de fluxo determinam a facilidade com que o pó fluirá quando o contêiner for esvaziado. Os pós podem ser classificados de acordo com sua fluidez:
- Pós de fluxo livre: fáceis de manusear, exigindo pouca assistência
- Pós coesivos: podem formar aglomerados e requerem auxiliares de fluxo
- Pós altamente coesivos: requerem soluções específicas, como fluidização, vibração ou até mesmo agitação mecânica
Testes específicos, como a medição doângulo de repouso, oíndice Carr ou o uso de células de cisalhamento, permitem que essas características sejam avaliadas com precisão.
Sensibilidade à umidade e higroscopicidade: os pós higroscópicos absorvem a umidade do ar ambiente, o que pode alterar suas propriedades físicas e químicas. Para esses produtos, são essenciais IBCs ou contêineres perfeitamente vedados e equipados com sistemas de desumidificação. A sensibilidade à umidade também pode determinar a escolha dos materiais de construção e das vedações.
Propriedades eletrostáticas: alguns pós, especialmente orgânicos e polímeros, podem gerar cargas eletrostáticas significativas quando manuseados. Essas cargas não apenas representam um risco de explosão em determinados ambientes, mas também podem afetar o fluxo do produto. Para essas aplicações, podem ser necessários contêineres aterrados ou feitos de materiais dissipativos.
Abrasividade e corrosividade: os pós abrasivos podem danificar progressivamente as superfícies internas dos contêineres, principalmente ao redor das válvulas e dos orifícios de drenagem. Para esses produtos, são recomendados materiais resistentes à abrasão ou revestimentos específicos. Da mesma forma, os produtos corrosivos exigem materiais adequados, comoaço inoxidável 316L ou revestimentos protetores.
2.2. Volume e taxa de produção
Uma avaliação precisa dos volumes de produção e das taxas de trabalho é essencial para dimensionar corretamente sua frota de IBCs e equipamentos associados. Essa análise deve levar em conta não apenas a situação atual, mas também as projeções de crescimento futuro.
Análise dos fluxos de produção: O mapeamento detalhado de seus fluxos de produção permite identificar os pontos críticos em que o uso de contêineres IBC trará mais valor. Essa análise deve considerar
- Volumes diários, semanais e mensais de pós manuseados
- Variações sazonais e picos de produção
- O número de referências e a frequência das trocas de produtos
- Os tempos de permanência do produto no processo de fabricação
Dimensionamento da frota de contêineres: o número de contêineres necessários depende de vários fatores interdependentes:
- O volume total de produtos em circulação
- O tempo de ciclo completo (enchimento, transporte, armazenamento, esvaziamento, limpeza)
- Tempos de espera entre os diferentes estágios do processo
- O número de diferentes referências manipuladas
O cálculo preciso desses parâmetros permite otimizar o investimento inicial e, ao mesmo tempo, garantir a disponibilidade suficiente de contêineres.
Modularidade e escalabilidade: as soluções modulares são particularmente adequadas para empresas com volumes de produção variáveis ou crescentes. Ao adquirir progressivamente contêineres IBC, você pode distribuir seu investimento e, ao mesmo tempo, adaptar-se às necessidades em constante mudança. Uma abordagem modular também pode ser aplicada aos equipamentos de enchimento e esvaziamento, com estações atualizáveis capazes de lidar com um número crescente de contêineres ao mesmo tempo.
Gerenciamento de fluxos físicos e de informações: A otimização do fluxo físico de contêineres deve ser acompanhada por um gerenciamento computadorizado eficaz. Os sistemas de rastreamento em tempo real permitem localizar cada contêiner, conhecer seu conteúdo e seu status (cheio, vazio, em limpeza). Essas ferramentas de gerenciamento facilitam o planejamento da produção e minimizam o risco de interrupções no fornecimento às linhas. Elas também contribuem para a rastreabilidade completa do lote, um requisito fundamental em setores regulamentados.
Tempos de troca otimizados: O uso de IBCs reduz consideravelmente os tempos de troca entre duas produções. Para maximizar esse benefício, é recomendável adotar as técnicas SMED (Single Minute Exchange of Die), preparando antecipadamente os contêineres necessários para a próxima produção.
2.3 Restrições regulatórias e de normas
As indústrias que lidam com pós estão sujeitas a estruturas regulatórias rigorosas que variam de acordo com o setor de atividade e a área geográfica. A transição para IBCs deve incorporar esses requisitos desde a fase de concepção do projeto.
Padrões sanitários e alimentares: no setor agroalimentar, os materiais em contato com alimentos devem estar em conformidade com regulamentos específicos, como o Regulamento Europeu (EC) nº 1935/2004 ou os padrões da FDA nos Estados Unidos. Os recipientes usados nesse setor devem ser feitos de materiais aprovados para contato com alimentos e projetados para limpeza e desinfecção eficazes. Os fabricantes devem fornecer “declarações de conformidade” atestando que seus contêineres atendem a esses requisitos. A implementação de um sistema HACCP (Hazard Analysis Critical Control Point, Análise de Perigos e Pontos Críticos de Controle) também pode exigir adaptações específicas aos contêineres e equipamentos associados.
Requisitos farmacêuticos e GMP: o setor farmacêutico é regido pelas Boas Práticas de Fabricação (GMP ). Essas diretrizes impõem altos padrões em termos de rastreabilidade, limpeza e validação de equipamentos. Os contêineres IBC usados nesse setor geralmente devem ter
- Superfícies polidas (acabamento Ra ≤ 0,8 μm para superfícies em contato com o produto)
- Conexões sanitárias em conformidade com os padrões (Tri-Clamp, BFM, etc.)
- Documentação completa, incluindo certificados de materiais, testes de integridade, qualificação de equipamentos, etc.
A validação da limpeza do contêiner é particularmente crítica e pode exigir a implementação de procedimentos específicos e testes analíticos para demonstrar a ausência de resíduos entre duas produções.
Segurança e meio ambiente ATEX: o manuseio de pós combustíveis ou explosivos exige a conformidade com a diretriz ATEX (ATmosphères EXplosibles). Esse regulamento europeu e seus equivalentes internacionais definem as medidas a serem tomadas para evitar explosões em áreas de alto risco. Para as aplicações em questão, os IBCs devem ser equipados com sistemas de aterramento eficazes e certificados. Certos componentes elétricos (sensores, sistemas de pesagem) devem ser projetados para operar com segurança nesses ambientes.
Rastreabilidade e integridade dos dados: Os setores regulamentados exigem rastreabilidade total de matérias-primas e produtos acabados. Os IBCs podem ser equipados com sistemas de identificação permanente (placas gravadas, etiquetas RFID) para rastrear seu histórico e conteúdo. No setor farmacêutico,a integridade dos dados também é crucial. Os sistemas computadorizados associados ao gerenciamento de contêineres IBC devem estar em conformidade com os princípios do Título 21, Parte 11 do Código de Regulamentações Federais (21 CFR Parte 11) ou doAnexo 11 das BPF europeias.
Padrões de transporte e logística: os contêineres IBC destinados ao transporte externo devem estar em conformidade com os padrões internacionais, como a certificação UN/ADR para o transporte de materiais perigosos. Suas dimensões devem ser compatíveis com os padrões de logística (paletes, racks de armazenamento, caminhões) para facilitar seu manuseio ao longo da cadeia de suprimentos.
3. Dimensionamento de equipamentos e integração de contêineres IBC
3.1 Escolhendo os contêineres certos
A seleção do tipo mais apropriado de contêiner IBC é uma etapa crucial para o sucesso de sua transição. Essa escolha deve levar em conta vários parâmetros técnicos, operacionais e econômicos.
Materiais de construção: A escolha do material depende principalmente da natureza dos produtos manuseados e das restrições de uso:
Aço inoxidável (304L, 316L)
Vantagens: durabilidade excepcional, alta resistência química, fácil de limpar, compatível com ambientes estéreis
Aplicações: indústria farmacêutica, química fina, indústria alimentícia de alta qualidade
Considerações: O 316L oferece melhor resistência à corrosão do que o 304L e é preferível para produtos corrosivos ou ambientes salinos.
Plástico de grau alimentício (PE-HD, PP)
Vantagens: baixo custo, leve, resistente a ácidos e bases
Aplicações: Processamento padrão de alimentos, produtos químicos não críticos
Considerações: Vida útil limitada, sensível a impactos e altas temperaturas
Contêineres compostos
Vantagens: Bom compromisso entre custo e desempenho, leveza
Aplicações: Produtos não críticos, transporte frequente
Considerações: Reciclabilidade às vezes complexa, durabilidade intermediária
Geometria e dimensões : Os IBCs estão disponíveis em uma variedade de formatos, geralmente adaptados aos padrões internacionais de logística:
Contêineres cúbicos/retangulares
Vantagens: Otimização do espaço de armazenamento, estabilidade
Considerações: Podem ter zonas mortas nos cantos
Contêineres cônicos
Vantagens: esvaziamento mais fácil, menos resíduos
Considerações: Uso menos otimizado do espaço de armazenamento
As dimensões padrão mais comuns baseiam-se em pegadas de paletes (1200x800 mm, 1200x1000 mm) com alturas variáveis, dependendo da capacidade.
Capacidades de volume: a escolha da capacidade deve levar em conta os volumes de produção, a densidade do produto e as restrições de manuseio:
500 litros: Adequado para pequenas séries de produção ou produtos com alto valor agregado
1000 litros: formato padrão que oferece um bom compromisso entre capacidade e manobrabilidade
1500-2000 litros: para produção de alto volume, exigindo equipamento de manuseio adequado.
Recursos específicos: Dependendo da aplicação, podem ser necessários recursos adicionais:
Sistemas integrados de vibração/fluidização
Benefícios: Fluxo aprimorado para produtos coesos
Aplicações: Pós finos, produtos sensíveis à sedimentação
Camisa dupla de aquecimento/resfriamento
Benefícios: Mantém a temperatura do produto, evita a condensação
Aplicações: Produtos sensíveis à temperatura, ceras Produtos sensíveis à temperatura, ceras, graxas
Isolamento térmico
Benefícios: Proteção contra variações externas de temperatura
Aplicações: Produtos sensíveis ao calor, ambientes sem controle de temperatura Produtos sensíveis ao calor, ambientes com temperatura não controlada
Sistemas de fechamento e vedação: A qualidade do sistema de fechamento é fundamental para garantir a estanqueidade e facilitar as operações:
Tampas com flanges parafusadas
Benefícios: Máxima estanqueidade, resistência à pressão
Considerações: Tempos de abertura/fechamento mais longos
Sistemas de liberação rápida
Vantagens: Fácil de usar, economiza tempo
Considerações: Necessidade de manutenção regular das vedações
Válvulas de fundo
Existem várias tecnologias (borboleta, esfera, guilhotina) com características específicas em termos de estanqueidade, capacidade de limpeza e resistência à abrasão. O diâmetro da válvula tem influência direta na taxa de fluxo de descarga e deve ser adaptado aos requisitos do processo.
3.2. Estações de enchimento e esvaziamento
A integração eficiente dos IBCs ao seu processo de produção requer estações de enchimento e esvaziamento projetadas especificamente para otimizar os fluxos de material e, ao mesmo tempo, garantir operações seguras e higiênicas.
Estações de enchimento: Os IBCs de enchimento devem ser projetados para preservar a integridade do produto e, ao mesmo tempo, garantir uma operação rápida e precisa:
Sistemas de dosagem
Dosadores volumétricos: para aplicações que exigem precisão média e altas taxas de fluxo
Sistemas de dosagem de peso: para aplicações que exigem alta precisão de dosagem
Sistemas combinados: combinando velocidade e precisão para grandes capacidades
Contenção e gerenciamento de poeira
Mangas de vedação infláveis para criar uma vedação estanque
Sistemas de exaustão local para capturar as emissões de poeira
Cabines fechadas com filtragem para produtos altamente ativos ou tóxicos
Compactação e densificação
Vibradores para otimizar o enchimento e reduzir o volume ocupado
Mesas de compactação para produtos sensíveis ao assentamento
Sistemas de desaeração para evacuar o ar preso
Estações de esvaziamento: O esvaziamento costuma ser o ponto crítico no manuseio de pós. OIBCFlow®02 é uma solução avançada para essa etapa:
Princípios operacionais
Conexão firme com a válvula do contêiner
Sistemas integrados de assistência ao fluxo
Controle preciso da taxa de descarga
Emissões de poeira minimizadas
Níveis de contenção
Contenção aberta: para produtos não perigosos com sistema de sucção
Contenção fechada: para produtos sensíveis ou ativos com transferência de vácuo/pressão
Contenção total: para produtos altamente ativos/tóxicos com circuito fechado e várias barreiras
Integração ao processo
Descarga direta em misturadores ou reatores
Alimentação de linhas de embalagem
Interface com sistemas de transporte pneumático ou mecânico
Pesagem e controle: a pesagem precisa geralmente é crucial:
Tecnologias de pesagem
Células de carga sob os pés (padrão)
Pesagem suspensa (maior precisão)
Sistemas de faixa dupla (capacidade e precisão)
Controle computadorizado
Gerenciamento de receitas e lotes
Registro de dados de pesagem
Interface com MES, ERP
Limpeza e descontaminação: a limpeza da estação é tão importante quanto a limpeza do contêiner:
Limpeza no local (CIP/CIP)
Bicos rotativos (enchimento)
Circuitos fechados (válvulas, conexões)
Sequências automatizadas (lavagem, enxágue, secagem)
Materiais e design
Superfícies polidas sem pontos cegos
Inclinações de fluxo otimizadas
Fácil acesso para manutenção
3.3. Automação e transporte
A automação do fluxo de contêineres IBC é uma etapa fundamental para otimizar sua produção geral. Ela não apenas reduz a intervenção manual, mas também melhora a rastreabilidade e a confiabilidade das operações.
Sistemas de transporte: a escolha depende da configuração, das restrições e do nível de automação:
Transportadores de roletes
Vantagens: Simples, robusto, baixa manutenção
Aplicações: Transferências horizontais, acumulação
Variantes: Rolos livres (gravidade) ou motorizados
Transportadores de corrente
Vantagens: Versatilidade, superação de diferenças de altura
Aplicações: Circuitos complexos, mudanças de direção
Considerações: Manutenção mais frequente
Veículos guiados automaticamente (AGV/AMR)
Vantagens: Máxima flexibilidade, adaptação dinâmica
Aplicações: Ambientes em mudança, conexão entre áreas remotas
Considerações: Maior investimento, infraestrutura de TI
Sistemas de posicionamento : A precisão é essencial para as operações automatizadas:
Paradas e guias mecânicas
Benefícios: Confiabilidade, simplicidade
Aplicações : Posicionamento grosseiro, parada
Sistemas ativos de centralização
Vantagens: Alta precisão, compensação de tolerância
Aplicações: Conexão automática com estações
Sensores e controles
Detecção de presença e identidade
Verificação do posicionamento correto
Proteção anticolisão e antiesmagamento
Identificação e rastreabilidade: um elemento fundamental para garantir a rastreabilidade e evitar erros:
Tecnologias de identificação
Códigos de barras (econômicos)
Etiquetas RFID (sem contato, armazenamento de informações)
Códigos QR (informações densas, omnidirecionais)
Informações rastreadas
Identificador exclusivo do contêiner
Conteúdo (produto, lote, quantidade)
Histórico (enchimento, armazenamento, limpeza)
Status e destino
Supervisão e controle: um sistema centralizado para um gerenciamento otimizado:
Funções essenciais
Exibição em tempo real (status, posição)
Gerenciamento de ordens de transferência e prioridades
Registro de movimentos e operações
Gerenciamento de alarmes e anomalias
Integração com sistemas existentes
Interface com o MES
Comunicação com controladores de processo
Conexão com sistemas de qualidade/rastreabilidade
Segurança operacional: A automação deve incorporar todos os aspectos de segurança:
Dispositivos de proteção
Barreiras físicas e áreas seguras
Detectores de presença e scanners a laser
Paradas de emergência e reinicializações seguras
Modos degradados e procedimentos de emergência
Possibilidade de intervenção manual
Procedimentos de recuperação de incidentes
Redundância de sistemas críticos
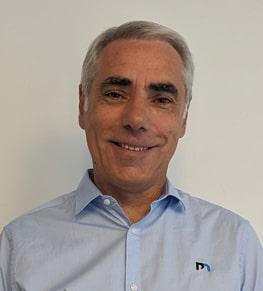
Você tem um projeto em mente ?
Estou aqui para aconselhá-lo e ajudá-lo com seu projeto.
Orlando, especialista em soluções modulares para pós industriais
4. Restrições e soluções para o esvaziamento de contêineres IBC
4.1. Características do produto que influenciam o esvaziamento
O esvaziamento eficiente dos IBCs é diretamente influenciado pelas propriedades físicas dos pós. Um entendimento completo dessas características permite prever possíveis dificuldades e implementar soluções adequadas.
Fluidez e coesão: A capacidade de um pó fluir livremente é crucial:
Classificação de acordo com a fluidez
Pós de fluxo livre (ângulo de repouso < 30°): esvaziamento fácil e regular
Pós de fluxo médio (ângulo de repouso 30-45°): podem exigir uma pequena ajuda
Pós coesivos (ângulo de repouso > 45°): requerem dispositivos de assistência
4.2. Soluções técnicas para esvaziamento eficiente
Existem vários sistemas para otimizar o esvaziamento de IBCs. Auxiliares de fluxo, como placas vibratórias ou fluidizadores de ar, evitam a formação de abóbadas e facilitam o fluxo do produto. Para pós sensíveis à umidade, recomenda-se o esvaziamento em uma atmosfera controlada.
4.3. Caso especial de produtos sensíveis
Os pós reativos ou altamente higroscópicos requerem atenção especial. O armazenamento hermeticamente fechado impede a absorção de umidade. O esvaziamento deve ser realizado em um ambiente confinado para evitar contaminação. Os sistemas de limpeza no local (CIP) garantem uma higiene impecável entre cada lote de produção.
5. FAQ: Respostas às perguntas mais frequentes sobre a transição para contêineres IBC
5.1. Quais são as principais vantagens dos IBCs em relação aos big bags?
- Redução da contaminação cruzada
- Integração mais fácil em linhas automatizadas
- Menos manuseio eintervenção humana
- Esvaziamento mais limpo e controlado
5.2. Como posso garantir o esvaziamento completo dos IBCs?
O uso de estações de esvaziamento adaptadas, como aIBCFlow®02, garante a extração total do produto sem perdas ou resíduos.
5.3. Os IBCs são adequados para todos os tipos de pó?
Sim, desde que você escolha o modelo certo e os acessórios adequados: válvulas, revestimentos internos, auxiliares de fluxo.
5.4. Quanto tempo dura um IBC?
Um IBC bem conservado pode durar várias décadas, reduzindo os custos operacionais.
5.5. Os IBCs podem ser integrados em uma linha de produção existente?
Sim, eles podem ser integrados gradualmente para substituir os big bags e melhorar a eficiência do processo.
Conclusão
Adotar contêineres IBC significa optar por uma produção mais limpa, mais flexível e mais automatizada. Essa transiçãootimiza a rastreabilidade, reduz a contaminação emelhora o gerenciamento de pó.
Você está envolvido no processamento ou aprimoramento de terras raras?
Entre em contato com nossos especialistas para projetarmos juntos uma linha de produção personalizada, segura e de alto desempenho.